Choosing the right protective coating for floors, walls, or other surfaces is a critical decision that can affect the durability, maintenance, and overall aesthetics of your project. Two of the most popular coating systems available today are polyurea and epoxy.
Both have unique properties and advantages that make them suitable for different applications. In this guide, we’ll explore the key differences between polyurea and epoxy coatings, examine their benefits and drawbacks, and provide insights into which might be the best fit for your particular project.
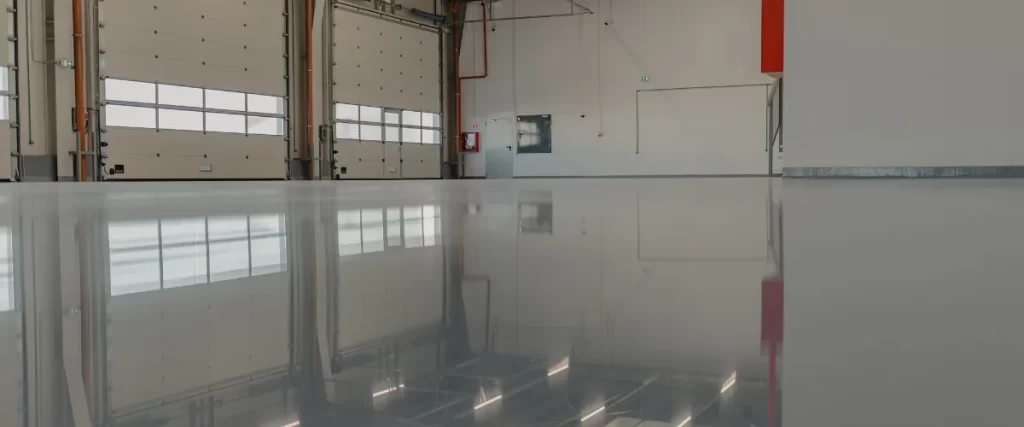
Overview of Polyurea and Epoxy Coatings
Polyurea coatings are known for their rapid curing time and exceptional flexibility. Developed initially for military applications, polyurea has evolved into a favored solution for industrial, commercial, and even residential settings.
This coating is typically applied using specialized spray equipment and cures in seconds, which is a significant advantage when minimal downtime is required. Polyurea’s elasticity allows it to better absorb impact and movement, making it ideal for areas that experience heavy traffic or where the substrate is subject to thermal expansion and contraction.
In contrast, epoxy coatings have been a stalwart in the world of protective finishes for many years. Epoxy is a two-part system consisting of a resin and a hardener that chemically react to form a rigid polymer.
Although epoxy takes longer to cure—usually several hours—it offers a very hard, durable finish that is highly resistant to chemicals, abrasion, and heavy use. The resulting high-gloss finish is aesthetically pleasing, which has made epoxy a popular choice in both commercial and residential applications.
Key Properties and Performance Characteristics
Curing Time and Application
One of the most noticeable differences between polyurea and epoxy coatings is their curing time. Polyurea’s rapid curing allows for a fast return to service. Because it cures within seconds, projects can be completed quickly with minimal disruption. This makes it particularly useful in industrial settings or high-traffic areas where downtime can be very costly.
Epoxy, on the other hand, offers a longer working time. The slower curing process—typically several hours—allows for a more meticulous application, which can be beneficial when applying to complex surfaces or when achieving a smooth finish is paramount.
However, this longer cure time also means that the area coated with epoxy must remain off-limits until the coating fully cures, which can extend the overall project timeline.
Flexibility and Durability
Flexibility is another critical factor where these coatings diverge. Polyurea coatings are highly flexible, which allows them to accommodate slight movements in the substrate without cracking.
This flexibility makes polyurea an excellent choice for areas that might experience structural shifts, heavy impacts, or severe temperature variations. Its ability to withstand thermal expansion and contraction ensures that the coating remains intact and performs well under fluctuating conditions.
In contrast, epoxy coatings are much more rigid. The hard, inflexible nature of epoxy gives it excellent resistance to abrasion and chemicals. However, its rigidity can be a disadvantage in settings where the substrate moves or shifts, as this can lead to cracking or delamination over time.
Therefore, epoxy is best suited for areas where the surface is stable and not prone to significant movement.
Environmental Resistance
Environmental factors such as UV exposure and moisture play an essential role in the performance of a coating. Polyurea is generally more resistant to ultraviolet (UV) light. This UV stability means that polyurea coatings are less likely to yellow or degrade when exposed to sunlight over long periods, making them an ideal choice for outdoor applications or areas with high UV exposure.
Epoxy coatings, while highly durable, are more susceptible to UV degradation. Over time, exposure to sunlight can cause epoxy coatings to yellow and become brittle, which might require periodic maintenance or re-coating. For indoor applications or environments with limited UV exposure, epoxy’s chemical resistance and aesthetic appeal make it an attractive option.
Chemical Resistance
When it comes to chemical resistance, epoxy coatings have a long-established reputation. Epoxy’s dense, cross-linked structure provides exceptional resistance to chemicals, solvents, and spills. This makes it a preferred choice for industrial environments, laboratories, and areas where chemical exposure is a concern.
Polyurea coatings also offer good chemical resistance, though in some cases they might not match the robustness of a high-quality epoxy system. However, polyurea’s performance in resisting impacts and abrasions often compensates for any slight differences in chemical resistance, particularly in high-traffic or dynamic environments.
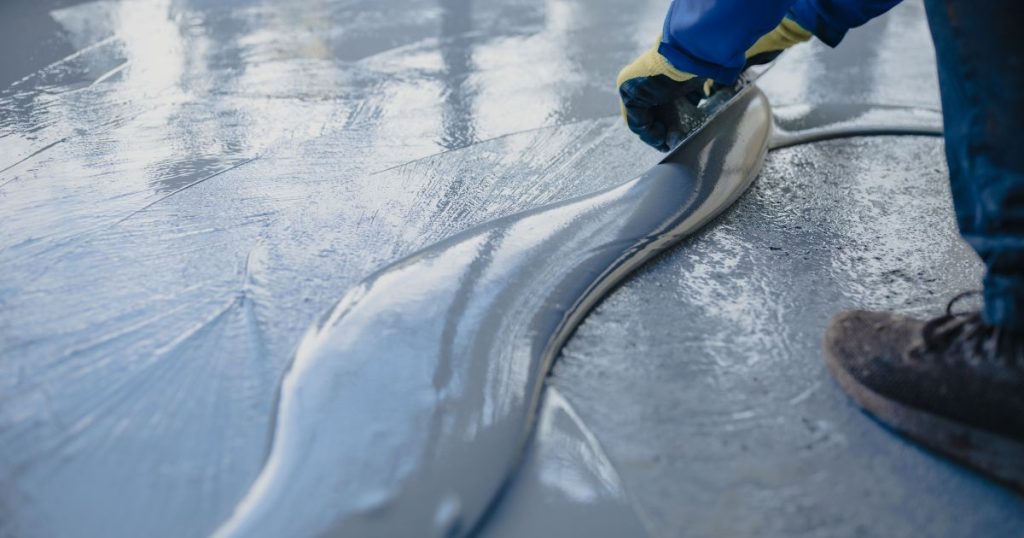
Comparison at a Glance
Below is a table summarizing the key differences between polyurea and epoxy coatings:
Feature | Polyurea | Epoxy |
Curing Time | Cures within seconds; minimal downtime | Takes several hours to cure fully |
Flexibility | Highly flexible; accommodates substrate movement | Rigid; may crack if the substrate shifts |
Application Method | Spray-applied using specialized equipment | Can be rolled or troweled on; versatile |
UV Resistance | Excellent UV stability; minimal yellowing | Susceptible to UV degradation and yellowing over time |
Chemical Resistance | Good overall; sufficient for many applications | Exceptional, ideal for harsh chemical environments |
Maintenance | Low maintenance; long service life | Durable but may require periodic re-coating |
Ideal Applications for Polyurea and Epoxy
Selecting the right coating depends largely on the specific requirements of your project. Consider the following factors when deciding between polyurea and epoxy:
- High-Traffic and Impact-Prone Areas:
For floors, garages, and industrial settings where impacts are frequent, polyurea’s rapid curing and flexibility are significant advantages. Its ability to quickly return to service with minimal downtime is a major selling point for busy environments. - Chemical and Abrasion-Resistant Needs:
In areas where exposure to harsh chemicals is a constant concern—such as manufacturing plants or chemical storage facilities—epoxy coatings excel. Their robust chemical resistance and hard finish make them ideal for these demanding applications. - Outdoor or Sun-Exposed Surfaces:
Polyurea’s excellent UV stability makes it the better choice for exterior surfaces or locations with significant sun exposure. Its ability to resist discoloration and degradation over time ensures a lasting appearance. - Cost and Budget Considerations:
While polyurea tends to be more expensive upfront due to its advanced formulation and specialized application, its long-term durability and low maintenance can justify the higher cost. Epoxy, with its more traditional formulation and broader availability, often comes at a lower initial price point but might incur additional maintenance expenses over time.
Cost Considerations
Cost is an important factor when deciding between polyurea and epoxy coatings. Polyurea generally commands a higher upfront cost because of its advanced technology and the need for specialized equipment during application. However, its long-term durability and reduced maintenance requirements can result in lower overall costs over the lifespan of the coating.
Epoxy coatings, being a more established and widely used option, are typically less expensive initially. This makes epoxy an attractive choice for projects with tighter budgets. However, the potential need for periodic re-coating or maintenance—especially in environments with high UV exposure or heavy chemical use—may increase long-term expenses.
Key cost considerations include:
- Initial Material and Labor Costs:
Polyurea tends to have higher material and labor costs due to its rapid application process and the need for specialized equipment. - Maintenance and Longevity:
Although epoxy may be cheaper to install, its rigid nature and susceptibility to UV damage may necessitate additional maintenance or reapplication over time. - Long-Term Investment:
Consider the overall lifespan and durability of the coating. A higher initial investment in polyurea might prove more cost-effective in high-impact or harsh environments, whereas epoxy might be sufficient for moderate-use applications.
Environmental Impact and Safety
Both polyurea and epoxy coatings have environmental and safety considerations that should be taken into account. Polyurea’s fast curing process generally results in lower emissions of volatile organic compounds (VOCs) during application, which is beneficial for both indoor air quality and the environment.
Epoxy coatings, while also effective, may emit higher levels of VOCs during their longer curing process, making proper ventilation and protective measures important during installation.
For projects where sustainability is a priority, researching low-VOC or eco-friendly formulations of both polyurea and epoxy can offer additional environmental benefits. Working with professionals who follow safety and environmental guidelines is essential to ensure that the installation process minimizes its ecological footprint.
Maintenance and Longevity
The longevity of your chosen coating will depend largely on proper maintenance. Regular inspections and prompt repairs of any minor damage—such as cracks or abrasions—can extend the life of both polyurea and epoxy coatings. Here are a few tips for maintenance:
- Clean Regularly: Use appropriate cleaning agents that do not degrade the coating. For epoxy, avoid harsh chemicals that could strip the finish.
- Inspect Periodically: Check for signs of wear, UV damage, or chemical exposure. Early detection of issues allows for timely repairs.
- Plan for Re-Coating: Even the best coatings will eventually require touch-ups or re-coating, particularly in high-traffic areas. Factor these potential costs into your long-term maintenance budget.

Top Manufacturers of Protective Coatings
When selecting protective coatings, choosing products from reputable manufacturers ensures durability, quality, and compliance with industry standards.
- Sherwin-Williams: Known for innovative solutions and a wide range of high-performance coatings for various applications.
- AkzoNobel: Offers sustainable and premium protective coatings with advanced technology for industrial and marine environments.
- PPG Industries: Renowned for delivering durable coatings tailored to intense chemical exposure and harsh environmental conditions.
- RPM International: Specializes in industrial coatings designed for long-lasting performance and enhanced surface protection.
- Jotun: Provides robust coating solutions with a focus on anti-corrosion and eco-friendly formulations for global markets.
Frequently Asked Questions (FAQs)
- What are industrial coatings used for?
Industrial coatings are primarily used to protect surfaces in challenging environments, such as factories, warehouses, and marine structures. They help prevent damage from factors like corrosion, chemical exposure, and extreme weather conditions, while often enhancing the appearance of the surface.
- How do anti-corrosion coatings work?
Anti-corrosion coatings create a protective barrier on metal surfaces, preventing moisture, oxygen, and other corrosive elements from reaching the material. Some coatings also contain inhibitors that actively slow down the corrosion process.
- Why is eco-friendly formulation important in coatings?
Eco-friendly coatings reduce environmental impact by minimizing harmful emissions, such as volatile organic compounds (VOCs), and utilizing sustainable raw materials. They align with global efforts to promote sustainability and comply with strict environmental regulations.
- What industries benefit the most from these coatings?
A wide range of industries use industrial and marine coatings, including construction, automotive, oil and gas, manufacturing, and shipping. These coatings are critical in maintaining the longevity and safety of equipment, structures, and vessels.
- How do I choose the right coating for my environment?
The choice of coating depends on factors like the type of surface, exposure to chemicals or moisture, temperature conditions, and required durability. Consulting with a coating provider, such as PPG Industries or Jotun, can help determine the best solution for a specific application.
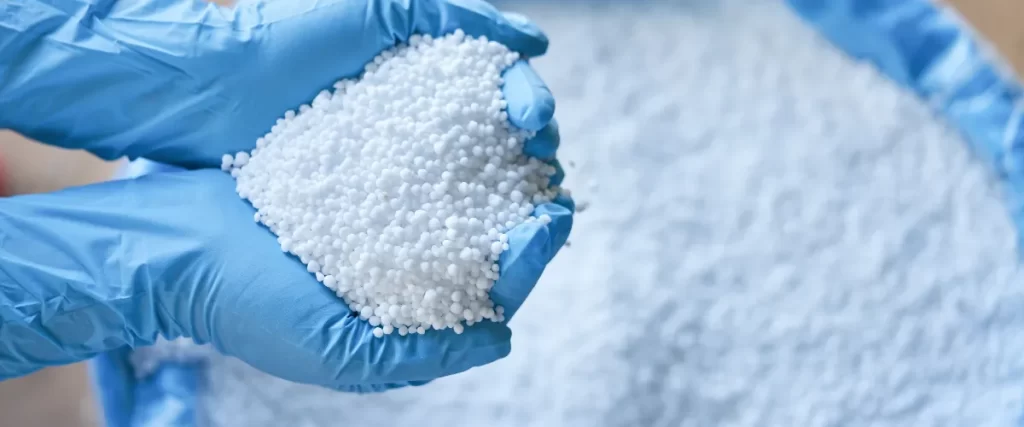
Why Choose Our Expertise
Our team has been delivering professional coating solutions for years, ensuring top-tier results. Work with the best to save money long-term. Contact us at (608) 839-0620 to begin your custom home building project today.